WING
フラウンホーファー、世界最大の熱可塑胴体製造に成功
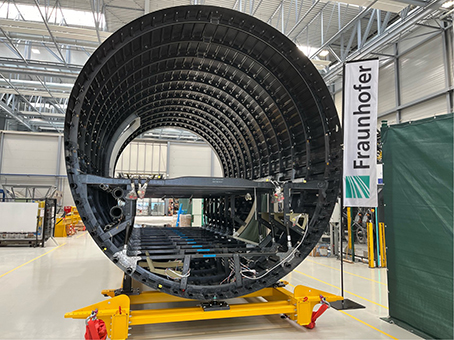
従来比10%軽量化、自動位置決めやレーザー接合など生産性向上
欧州最大の応用研究機関であるフラウンホーファー研究機構が、世界最大の熱可塑性CFRP航空機胴体の自動生産のための新たなアーキテクチャを実寸大で実証することに成功した。フランホーファー研究機構によれば、EUが資金を拠出している欧州の「クリーンスカイ2/クリーン・アビエーション・プロジェクトの「大型旅客機」(LPA)の一環として、自動化した位置決めと接合プロセスを用いて、「多機能胴体実証機」(MFFD)の実物大の上部シェルと下部シェルを結合することに成功した。
航空機の環境適合性を深掘りしていくことが求められているなか、新たな推進技術はもちろん、より軽量な構造、さらには製造コストにも焦点が当てられている。とりわけ熱可塑性CFRPが注目されており、CFRPを十八番の技術とする日本の素材産業も、その研究開発と生産性向上に力を入れている。
フランホーファーの研究でも熱可塑CFRPを活用し、熱可塑性CFRP材料からフルスケールの胴体セグメントを製造する研究プロジェクトを推進。その実現可能性のみならず、生産効率および経済的なメリット・デメリットを評価した。
※写真=熱可塑性溶接で結合された航空機胴体の実寸大セグメント(提供:フランホーファー)
※この記事の概要
・熱可塑CFRP製胴体でどの程度軽量化・コスト削減?
・左側をレーザー溶接、右は超音波で溶接
10台のロボがサブミリ単位で位置合わせ など
・