WING
早大、電気パルス直接放電で炭素繊維効率回収
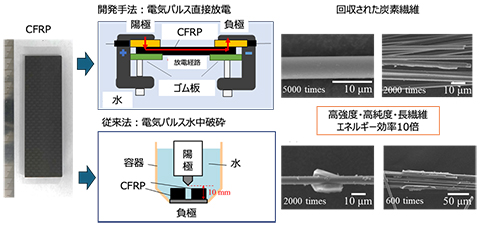
回収繊維は元の強度の81%キープ
早稲田大学理工学術院の所千晴(ところ・ちはる)教授らの研究チームが、電気パルス直接放電法を用いて、炭素繊維強化プラスチック(CFRP)から炭素繊維を効率的に回収する手法を開発することに成功した。
主要な構造がCFRP製の787ドリームライナーやA350XWBといった現役の低燃費機材の退役が、そう遠くない将来進んでいく見通しにあるなか、航空業界は大量に使用されたCFRPをいかに効率よく炭素繊維を回収することができるのか、技術開発を進めていくことが課題の一つだ。航空機産業のみならず、自動車、風力発電、スポーツ用品など、軽量高強度を必要とする他産業でもCFRPの利活用は進んでいる。一方でその効率的なリサイクル技術は未だ十分とはいえず、とりわけ樹脂マトリックスから炭素繊維を分離するプロセスが課題となっている。
現在、CFRPを十八番とする日本国内の様々なプレイヤーはもちろんのこと、海外でもCFRPのリサイクル技術の研究開発が進められているなか、早稲田大学の研究チームは今回、加熱や薬剤を必要とせず、従来の破砕法に比べて長繊維で、加熱法に比べて高強度の炭素繊維を回収可能な技術を開発した。
この研究は所教授のほか、同大学大学院院創造理工学研究科博士課程1年の佐藤啓太(さとう・けいた)氏、同大学カーボンニュートラル社会研究教育センターの犬束学(いぬつか・まなぶ)准教授、同大学理工学術院の小板丈敏(こいた・たけとし)講師らの手によるもの。
従来のCFRPのリサイクル方法としては、粉砕、熱分解、化学分解などが検討されてきたが、例えば粉砕では炭素繊維が短くなり、その強度が著しく低下してしまう。熱分解すると樹脂を高温で燃焼させることで分離が可能だが、CO2排出の懸念および炭素繊維の強度が50~85%低下してしまうという問題があった。さらに化学分解法の場合、有機溶媒を使用して樹脂を溶解するため、高価な溶剤・設備が必要なほか、環境影響が課題とされてきた。